Originally published in The Clarinet 49/3 (June 2022).
Printed copies of The Clarinet are available for ICA members.
Equipment Matters
Women in Clarinet Repair
by Sarah Manasreh
“Equipment Matters” features instrument repair technicians and mouthpiece experts writing on a variety of topics related to repair and maintenance. Please contact [email protected] with suggestions or contributions.
I can vividly remember the first time playing my clarinet after an expert repair person had worked on it. The feeling of the clarinet doing exactly what it was designed to do was exhilarating, like climbing behind the wheel of an expensive sports car. Moreover, knowing that some of the issues weren’t just me was truly relieving. It always felt as if repair technicians honed magic that could transform the experiences of every clarinetist. In this interview, I explored the story behind the magic with some of the leading women repair technicians in the United States – Melanie Wong, Heather Karlsson and Kristin Bertrand – to learn more about their career paths, interests and advice for clarinetists.
Sarah Manasreh: What was your path to a career in repair and equipment? What experiences drew you into the profession?
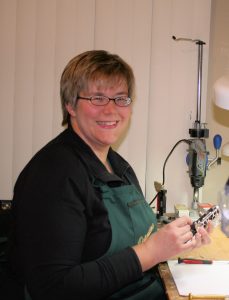
Heather Karlsson
Heather Karlsson: I was first introduced to repair as an undergraduate. My clarinet professor, Dan Hearn, impressed upon us the importance of taking good care of our equipment. Since I showed an interest, he showed me how to do some pretty basic maintenance things so I could take better care of my instrument. I also did some work with the university building operations manager who oversaw instrument maintenance at the school of music. I didn’t pick it up again until after graduate school. I signed on as an apprentice repair technician at a local music store. While there, I had the opportunity to work with Tom Ridenour. He was a profound influence on my understanding of the clarinet and clarinet playing, and I’m grateful to have worked with him. Through him I got to meet a lot of people I otherwise would not have met and had experiences I otherwise would not have had. When we parted ways, I took a job as a quality control consultant for a factory in Beijing, China. This was also quite educational. From there, I decided to open my own shop, and I’ve been doing that ever since.
Kristin Bertrand: I was, oddly, almost singularly driven to become a woodwind repairperson! I knew from the time I was in high school that I really wanted to learn. When I would visit the repairperson with my own instruments, I adored the racks of pliers and all the tiny drawers full of bits and pieces.
I grew up in a small snowy town in upstate New York in a household that is equally musical and mechanical. When I was an undergrad student at McGill University, I had a surgery on my left pinky finger to correct a problem with a crunchy tendon. The surgery didn’t go well. I lost all muscle tone, and the tendon malfunction was the same as before. My poor pinky was skinnier than a pencil and it became clear that a career in performance was unlikely. I had approached all of the high-end shops in Montreal looking to learn instrument repair but was turned down. I tried student teaching and it wasn’t for me.
After I finished my bachelor’s degree I moved to Los Angeles and was offered an apprenticeship at RDG in Los Angeles, only to find out that Bob Gilbert (the original owner of RDG) hadn’t consulted his repair staff before making the offer! I guess he did this often, so the repair staff, John Peterson and Tom Yaeh, were pretty annoyed. Of course, Bob should have asked them first! But, after a few initial repair lessons with the great Francois Kloc (yes, he started out as a technician too!) it became clear that I was very serious, dedicated, and well suited to the profession, and John and Tom went above and beyond to make sure I was well trained. I can never thank them enough for their time and expertise. They were so incredibly generous and patient. I stayed at RDG for five years until my husband’s job was transferred to New York, and except for a short stint in Washington, D.C., we’ve stayed in New York ever since.
Melanie Wong: Throughout my undergrad years as a music performance major, I had always wanted to learn repair. I don’t know why; it was just something I found interesting and thought I might be good at. I considered myself a “crafty” person and really had no idea what repair really entailed. There were two active and highly respected female repairers when I was in college – Kristin Bertrand and Shelly Tanabe –
and when I went in for repairs, I asked both how they got started. They both explained how they had apprenticed under master technicians, and I decided that I would try to go that route myself. I asked so many people for apprenticeships throughout my undergraduate and graduate studies and was declined by each and every one. Finally, I called Mark Jacobi when I was nearing the end of my schooling and after a few months of nudging he finally agreed to teach me. I really got quite lucky because at the end of the day, he was really the best teacher for me, and I probably wouldn’t have continued in the field had I learned elsewhere.
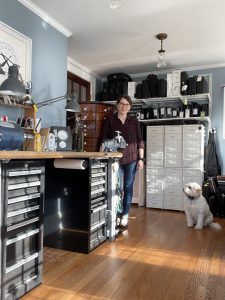
Kristen Bertrand
SM: What are some of your areas of expertise? What type of clientele do you serve?
HK: Repairs on members of the clarinet family. It’s what I do most of the time. In the past I’ve served the up-and-coming performance majors and professionals, but lately I’ve been dealing more with enthusiasts, retirees, and the like. I’ve also dealt with school districts, which – if you live in Texas, you can imagine what horrors have been visited upon my bench in the name of marching band.
KB: My areas of expertise are the clarinet, oboe and bassoon families. I specialize in high-end professional repair, including crack repair, tuning, voicing, and custom keywork. I have a special affinity for bass clarinet repair, which is grueling to do, but I love it anyway! Over time I have expanded the shop to also include my own custom products and new professional instruments.
Being a one-person shop in a major city I try to limit myself to high-end instruments of recent manufacture. My clientele are professional musicians and dedicated upper-level students. I commonly work for members of the New York Philharmonic, the Met Opera, City Ballet, Orpheus Chamber Ensemble, Imani Winds and of course Broadway. I’m very proud to serve these fine, hardworking people and help them to be the very best they can.
MW: I’m considered a clarinet specialist, meaning I only work on clarinets. Anything in the clarinet family, that is. I do all the basic work you think of – changing pads, springs, corks, fitting keys, etc. I also do crack repairs, including traditional steel pinning, carbon pinning, carbon fiber banding, and tone hole replacements. I do custom keywork and build mechanisms, like low F correctors and key extensions. But if I had to say what I’m most “known” for, it’s probably for both my new instrument setups and my tuning and voicing work. One of the things I love to do most is sit with clients and help them understand the tuning of their instrument and what can be changed and how we can achieve the best results for them, whether that be through modifications to the instrument itself or through equipment changes, strategic tuning ring placement, etc.
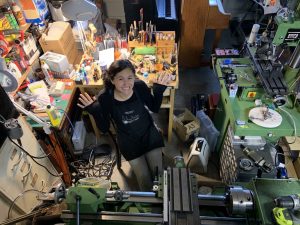
Melanie Wong
SM: What has been your most memorable repair?
HK: An Eppelsheim contrabass clarinet. It was so heavy that it needed a special stand and I had to crawl up under it to work on it like I was working on a car engine. It was a thing of beauty, but I did wonder about the practicality of such a heavy instrument. It was made of brass with a black lacquer finish, and the keys were gold plated, if I remember correctly. I was terrified of damaging the lacquer.
KB: My most memorable repair was a time that I thought I had made a big mistake, and it happened about 12 years ago at the Buffet showroom when I had five clarinets arrive at the same time for crack repair. Crack repairs are always an emergency; nobody schedules a future crack repair, how could they? I decided to do an assembly-line approach, first disassembling them all, then pinning, tone-hole inserts, pad replacement, and finally reassembly. If you’ve ever visited my shop, you’ll know that I’m very organized and tidy, so working like this wasn’t very difficult.
I finished all the repairs and one by one they went back to their owners, but something was funny about the very last one. The bridge keys didn’t line up well, and the playtest felt weird. The client was due to arrive in 20 minutes to pick it up, and I was doing my best to make it as good as I could before they arrived when I noticed that the upper and lower joints had different serial numbers. A closer inspection revealed that the top and bottom were different models also, the upper was a Buffet Vintage model and the lower joint was a Festival! It appeared that I had mixed up the top joints during the assembly-line crack repair, but this was the last one to go out the door, so I had no idea who had the proper top joint to this bottom joint and there was no time to make it right.
The client arrived shortly after, and there was nothing left to do but own up to my mistake. When he arrived, I said to him, “It appears that the upper and lower joints of this instrument have different serial numbers.” And he said, “I know, it was like that when I bought it!” I hadn’t made a mistake at all. He brought it in that way!
I’ll also never forget the repairs I’ve done for special clients who have since passed away. I worked on Mitchell Lurie’s clarinet, and when he played it and told me he loved it I nearly melted. Jim Ognibene was a favorite client also. He was a lot of fun to be around! I remember setting up his new bass clarinet and tuning it just how he liked it, then attending the Met Opera that same evening and hearing his exquisite playing.
MW: This is tough, but my mind takes me to the first few low F correctors I ever built. My first few correctors were for clients who are good friends of mine and there were more than a few very late nights involved! They would
keep me company throughout the process – bringing me coffee and dinner, sleeping on the couch, cracking jokes and just otherwise providing moral support. There were so many mishaps and re-dos but looking back it was actually a lot of fun and I will be forever grateful that they trusted me with their instruments and had faith that no matter what happened along the way, it would all be good in the end!
SM: What’s something that you wish clarinetists would do (or stop doing) for their instruments?
HK: Please observe basic hygiene. Wash your hands before you play. Wipe your instrument off after you play. Brush your teeth before you play. Don’t eat while you play. And for the love of all that is right and good in the world, swab your instrument! These simple acts will go a long way toward keeping your instrument in good shape.
KB: I think most technicians would agree with me that while we don’t mind doing some cleaning, we’d like to get past that part faster so that we can get to the more technical aspects of the repair that will really improve the instrument! Players could help us out with this by brushing their teeth before playing, dusting the instrument frequently with a long bristle paintbrush, and putting it away in the case religiously. Don’t let your cat nap in your open case. Don’t let reeds or ligature screws or other flotsam float around in the case.
Similarly, I wish that clarinet case manufacturers would design a place for the mouthpiece to live that is separate from the rest of the instrument. The sulphur in the hard rubber of the mouthpiece tarnishes silver plate dramatically, especially if the case is left closed. While I don’t mind polishing instruments, my time is much better spent on mechanical instead of cosmetic work.
MW: One of the biggest things, particularly with pre-professional clarinetists, is just making the time to get your maintenance done, and having that time not be very close to upcoming auditions or performances. If you’re thinking of getting an overhaul done, this is something you’d do well before your recital, not a week or even just days prior. You want to have ample time to get used to any big changes to your instrument well before you play something important on it. You also want time to work with your repair person to make any necessary tweaks after the fact. It helps to remember that we repairers are only human. We try our absolute best, but we also make mistakes, miss things or set things up differently than you might want. So, along these lines, if something isn’t quite right after your repair, give the repairer a chance to make it right! Explain your issue to them without anger or casting blame. You will typically find that they are more than willing to do what they can to help you.
SM: What is the most satisfying part of your work?
HK: I think the most satisfying thing I ever did was seek out a plateau system clarinet for an older gentleman who had Parkinson’s. He was heartbroken that he couldn’t play his beloved clarinet in church anymore, and had to switch to saxophone, but the saxophone was so heavy that it exacerbated his nerve damage. Jeff Smith at J. L. Smith was cleaning out some stuff he had, and he had a few Noblet plateau key clarinets, so I got one and fixed it up for the guy. I still have the answering machine message from him about how happy he was that he could play again.
KB: I get a lot of satisfaction from custom keywork for people with special needs. I’ve customized instruments for people missing parts of their digits. I recently added extensions to a BÌ for a client with deformed hands. One time I converted an entire clarinet to plateau system for a university professor in his 80s who was having trouble covering the open tone holes. I even burned a hole in the carpet at the Buffet showroom while soldering it (sorry Francois!). He was so happy when he picked it up and called me the following week to play it for me. Sadly, he passed away unexpectedly soon after that, but I’d like to think that he had a few good weeks with it!
I also love doing tuning and voicing. It’s great to help a player get exactly what they need from the instrument. There’s a lot of trust involved. It took years to develop, but I finally know which questions to ask so that I take the approach that gives the most benefit.
And I’m not going to lie, I do look forward to crack season every year. It’s hectic and fussy and throws my schedule for a loop but I love making the crack repairs look and work just right.
MW: For me, the best is when I’ve fixed a young player’s clarinet for the first time and their eyes get very wide as they realize how much easier it is to play now that the instrument is sealing, balanced and just otherwise living up to its potential. They realize the hours and hours of practice they’ll no longer have to do on certain passages because it was the instrument not working well, rather than something in their technique. That’s always a great feeling. Of course, I feel the need to also say, it won’t always be the instrument! Sometimes the answer really is that you just need to practice!
The other thing I’ve loved is working with professionals on tuning and voicing. I’ve been so lucky to work with some of the greatest clarinetists of our time and learn so much from just having them in the shop and learning their needs and priorities. It’s amazing what you can learn from listening to someone’s warmup or how they test their newly repaired instrument. Even just watching how they place their fingers on the instrument can bring a lot of insight, not to mention seeing what equipment they use, what they’re trying and why, and hearing their thoughts on all the myriad accessories out there.
SM: Do you have any advice for people wanting to get into the profession of repair?
HK: It’s not glamorous. It’s not easy. You will burn yourself, stab yourself, cut yourself, catch respiratory infections from disgusting instruments, and, if you’re not careful, lose chunks of your fingers. It’s not a way to “get rich quick,” contrary to some statements you might find on the internet. There is a high rate of burnout in the profession, and the work is, by and large, horrifically tedious. In my opinion, the better you can play an instrument, the better your repair work will be. Quality screwdrivers are an absolute must, as is a good chair for proper posture. I would also recommend having a strong stomach, because you would not believe some of the nastiness that can come out of some people’s instruments.
KB: There is a definite deficit of repair people in New York and around the country. If you love tools and minutiae, and have a steady hand, this might be a good career for you. The initial time and monetary investment is relatively low compared to other career paths, and you can attend a one-year repair school or even an online course and know for sure if you’d like to continue. Even if you decide not to make it your career, you’ll still be a better player, teacher and colleague with the mechanical understanding you’ve gained. Also, I’ve found that there are paths for different personality types when it comes to instrument repair. I love to obsess over just one or two instruments for the whole day, sometimes a whole week, so high-end professional repairs suit me well. But if that would drive you nuts, you can specialize in school music repair where you typically work on 10 or 15 more varied instruments each day.
This is my 22nd year working in woodwind repair, and I feel lucky every day that I get to work for this community, doing the work I love.
MW: I think the main thing is to take it seriously. Understand that you’re learning a craft and an art. Just like learning to play your instrument at a high level, learning repair takes the same dedication and practice. You won’t become a repair guru in a matter of weeks or months. If you do enter the profession, you will become a lifelong learner. There is no repair person that “knows it all.” We are constantly learning and updating our views and practices. Be open to lots of different perspectives and add as many techniques and tricks to your toolbox as you can. There are so many different yet equally valid ways to fix an instrument, and it will help you to be curious. And once you’re on your journey, please remember: If you see an instrument come across your bench from a famous repair person, try to understand what they did and why, even if it’s different from what you’re currently learning from your own teacher. Don’t be quick to say work is bad just because it looks different than what you’re used to. Being curious and learning to understand different ideas within our industry will always help you improve your craft!
About the Writer
Dr. Sarah Manasreh is assistant professor of clarinet and music theory at the University of Wisconsin – Stevens Point and principal of the La Crosse Symphony Orchestra. Sarah is an active member of the ICA and was recently appointed editor for The Clarinet [Online]. She has formed several student-led groups at UWSP that promote wellness and equity in music. She received her D.M.A. from Michigan State under the tutelage of Elsa Ludewig-Verdehr, M.M. from the Royal Northern College of Music, and B.M. from Florida State University.
Comments are closed.